Understanding the Cost of Metal Coatings: A Practical Guide
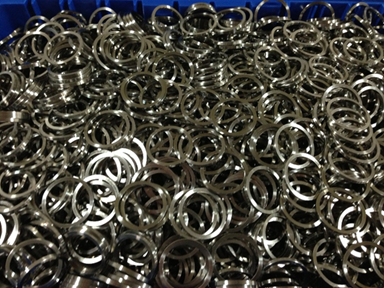
When selecting a metal coating for your application, cost is always an important factor. While it might be tempting to choose the least expensive option, it’s critical to understand the trade-offs in durability, performance, and long-term value. Here, we explore how the cost of different coating types compares, particularly focusing on our PEN-TUF® process—electroless nickel with PTFE.
Relative Coating Costs
There are many effective solutions for environments that require corrosion protection and where the parts are not subject to abrasion. They are relatively low in cost but are often quite effective. Examples include:
- Chromate conversion (chem film)
- Black oxide
- Manganese phosphate
- Zinc plating
As performance requirements increase, so does the need for a higher quality coating. For maximum corrosion protection and superior electrical conductivity, precious metal plating is often the best option:
- Gold plating
- Silver plating
Of course, precious metal plating can be costly, especially since gold is currently trading at over $3,000 per troy ounce.
PEN-TUF®
Pen-Tuf Pentuf® is an electroless nickel plating process and it is much more complex than simple immersion coating like chromate conversion. Instead of a rectifier, the power source for electrolytic plating, electroless nickel plating utilizes a chemical catalyst to initiate the plating reaction.
PEN-TUF® is formed by the addition of a PTFE dispersion to the electroless nickel tank. Nickel and PTFE are then co-deposited throughout the plating process delivering a uniform coating that is especially effective for high abrasion environments.
Pen-Tuf® is conductive, it can be applied with tight tolerances, and at a wide variety of thicknesses. And, in contrast to plating with precious metals, Pen-Tuf® and electroless nickel are highly cost effective.
Proven Performance: Tested and Certified
Cost should always be weighed against performance. PEN-TUF® is applied to meet AMS 2454, a widely recognized industry specification guiding rigorous quality control requirements. For example, salt spray (or salt fog) corrosion resistance testing is performed to simulate long-term exposure to harsh environments and measures how long a coating can resist corrosion.
We don’t just say it passes—we prove it. For example, in working with Lockheed, we submitted not just certificates but actual test panels to validate 500-hour corrosion resistance claims. In fact, PEN-TUF® regularly meets or exceeds the most stringent service classes.
- SC5 Service Class (1,000 hours)
- SC6 Service Class (2,000 hours)
These results confirm our commitment to verifiable performance.
Quality Beyond the Spec Sheet
At AST, we go beyond simply running a process according to a spec. We routinely validate our coatings against the quality control provisions of those specs. Each month, in-house and outside testing on PEN-TUF® and our other finishes to ensure consistent compliance. That commitment means our clients, whether aerospace giants, high-performance manufacturers, or conscientious commercial producers, can trust that our coatings deliver what we promise—not just in paperwork but in real-world performance.
The Bottom Line
While PEN-TUF® may not be the cheapest option on the market, it offers a compelling balance between cost, performance, and longevity. For applications where failure isn’t an option and precision matters, it delivers exceptional value. Want to know if PEN-TUF® is right for your next project? Let’s talk.